Blog especializado de intralogística
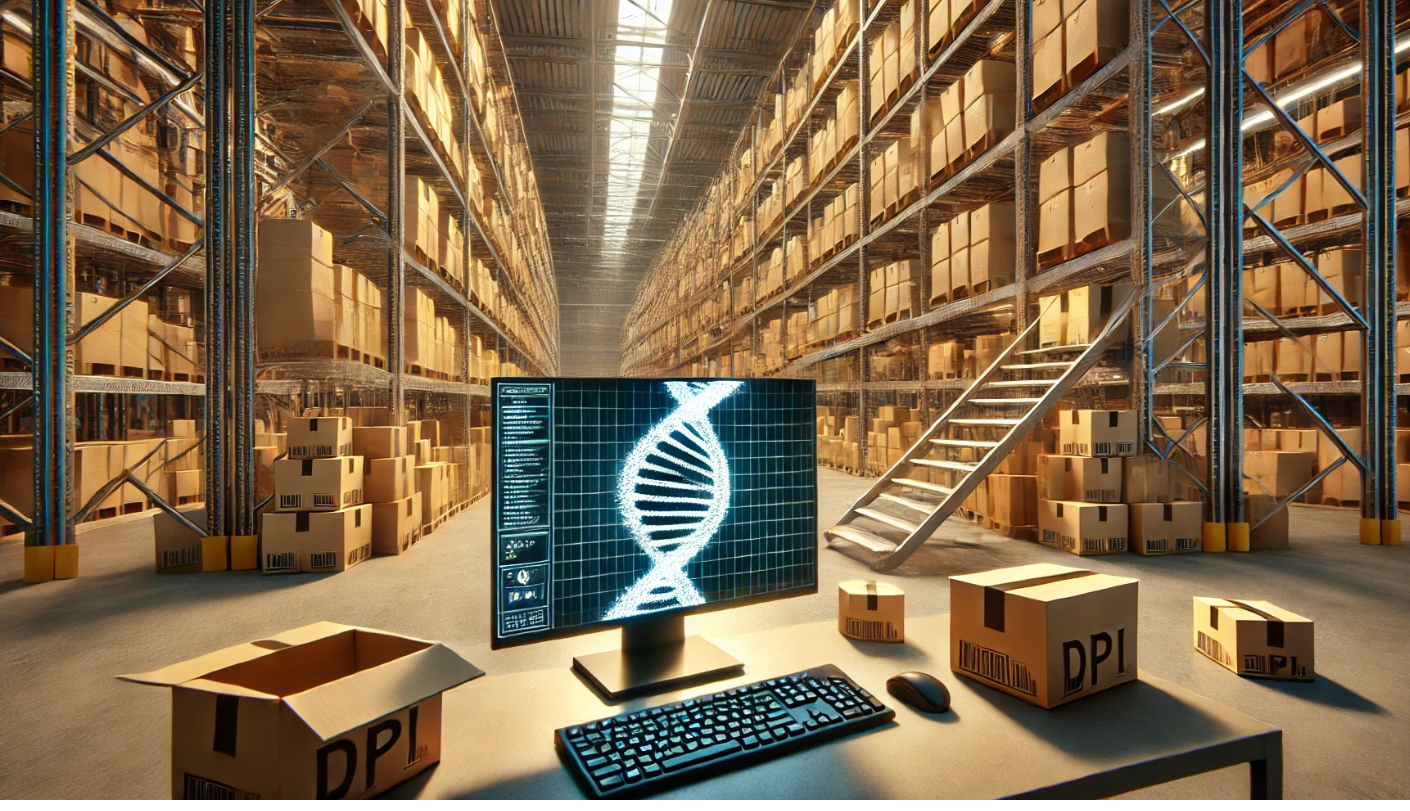
En el competitivo mundo de la logística, la eficiencia es la clave. La rapidez en la preparación de pedidos, la reducción de movimientos innecesarios y una correcta organización del almacén pueden marcar la diferencia entre un servicio logístico excelente y uno que simplemente cumple. En Dimensia, como empresa especializada en ingeniería logística, hemos desarrollado una solución innovadora para llevar esta eficiencia al siguiente nivel: DPI (Dimensia Posicionamiento Inteligente) . DPI es un programa basado en inteligencia artificial , concretamente en el uso de algoritmos genéticos , que permite ubicar los palets en el almacén de manera óptima . Su objetivo es claro: minimizar el número de movimientos necesarios en la recogida de pedidos, ya se trate de palets completos o de picking de cajas. Más allá del ABC: inteligencia contextual. A diferencia de los sistemas tradicionales que basan su lógica de ubicación en el análisis ABC (centrado únicamente en el volumen de ventas o de líneas de cada artículo), DPI va mucho más allá. ¿Por qué? Porque sabemos que el comportamiento real de los pedidos en un almacén es mucho más complejo. DPI tiene la capacidad de detectar correlaciones entre artículos , es decir, identifica qué productos suelen pedirse juntos, independientemente de su volumen individual de ventas. Así, un artículo de baja rotación (tipo C), si aparece de forma recurrente en pedidos junto a artículos A, será tenido en cuenta para una ubicación estratégica cercana. Esto permite un diseño logístico mucho más eficiente y ajustado a la realidad operativa del almacén.
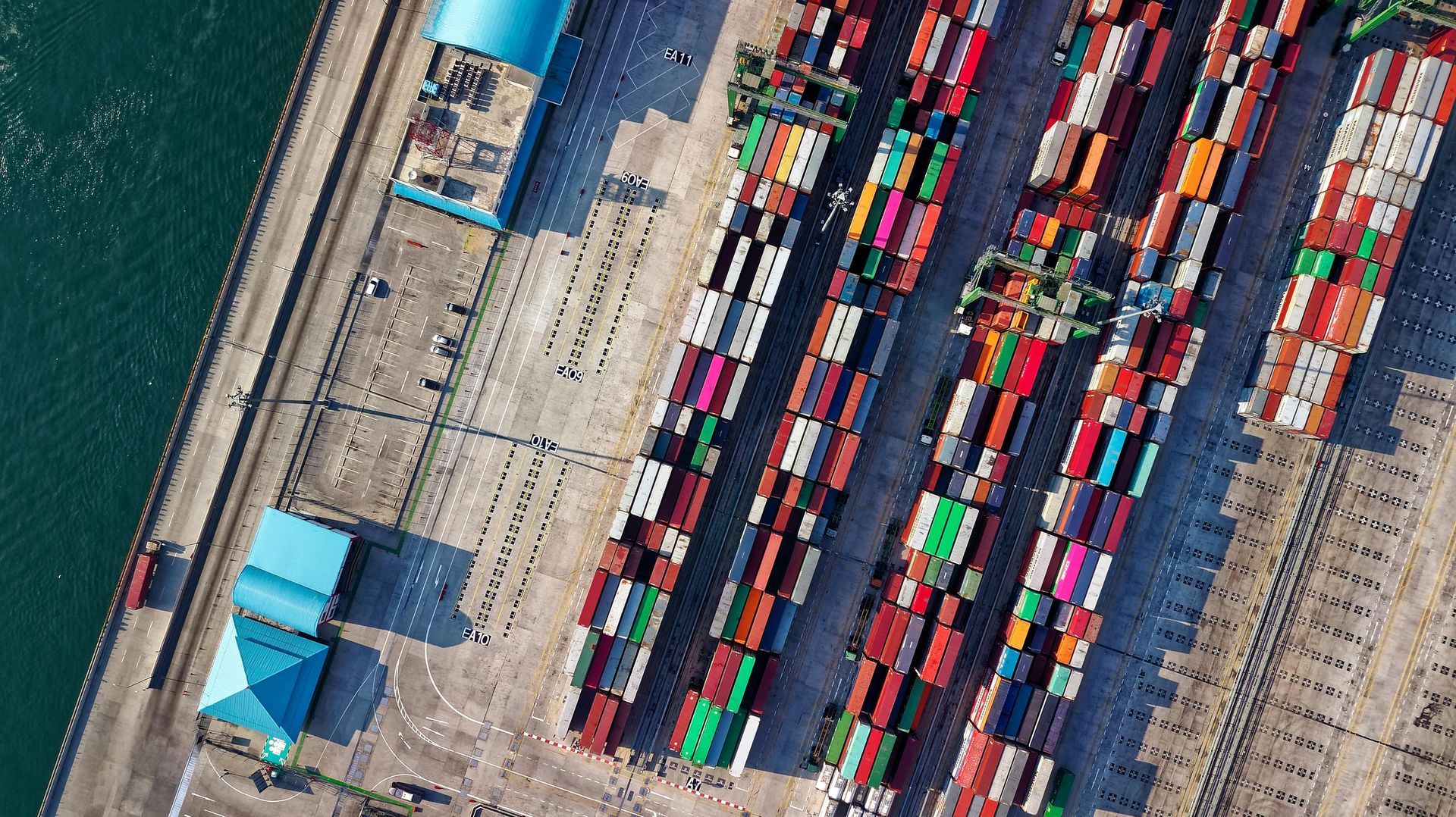
En el contexto globalizado actual, donde el comercio internacional y la logística son pilares fundamentales de la economía, maximizar el aprovechamiento del espacio en los contenedores marítimos se ha vuelto una prioridad estratégica. No se trata únicamente de reducir costes de transporte, sino también de minimizar el número de envíos, reducir la huella de carbono y garantizar la seguridad de la mercancía durante el trayecto. Desde Dimensia , y fieles a nuestro compromiso con la ingeniería logística de alto nivel, hemos desarrollado DICONTAINER , un programa avanzado para la planificación, simulación y optimización de la carga en contenedores marítimos , pensado para aportar precisión, eficiencia y control total en cada operación.
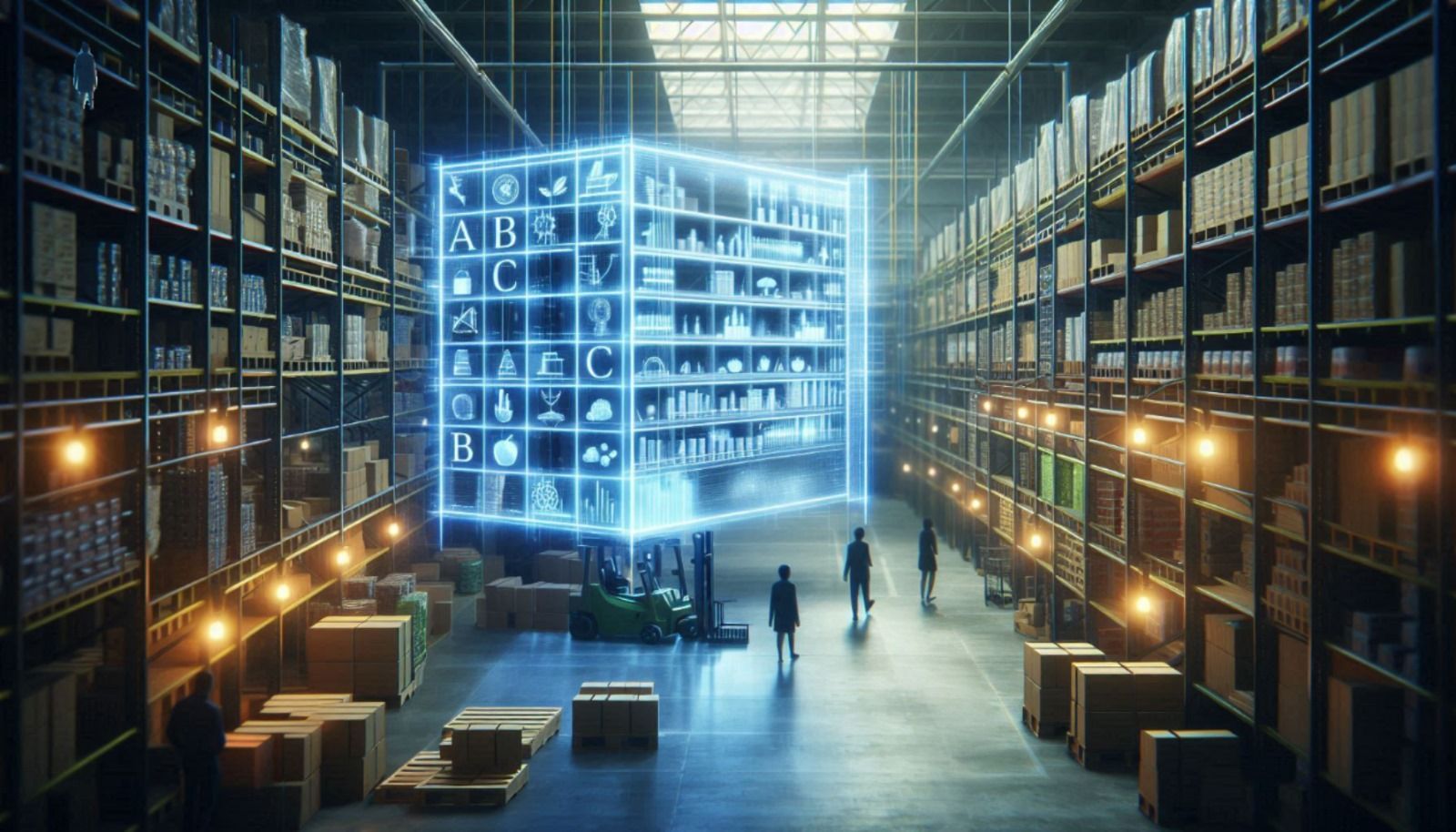
El problema del hilo rojo: Posicionamiento inteligente en almacenes. La eficiencia en la gestión de un almacén es fundamental para optimizar recursos y mejorar el servicio a nuestros clientes y uno de los principales factores que incrementan esa eficiencia es, sin duda, una óptima distribución de los diferentes artículos en el almacén , que nos permita minimizar el número de movimientos en la preparación de pedidos. Tradicionalmente , el posicionamiento de las diferentes referencias en el almacén se ha basado en el análisis ABC de líneas o ventas, o en un mix de ambas. El análisis ABC es una técnica de gestión de inventarios basada en el principio de Pareto , que establece que aproximadamente el 20% de los productos representan el 80% del valor o del movimiento del inventario. Esta clasificación divide los artículos en tres categorías: Clase A : Productos de alta importancia, que representan un pequeño porcentaje de las referencias, pero una gran parte del valor o volumen de ventas. Clase B : Productos de importancia intermedia, con una relación equilibrada entre cantidad y valor. Clase C : Productos de baja importancia, que comprenden la mayor cantidad de referencias, pero con un impacto menor en el inventario. Una fórmula mejorada, con respecto al análisis ABC, es la utilización del método del k-ésimo mejor vecino (o simplemente “k-ésimo”) que es algo más complejo, pues busca ordenar los artículos por diferentes variables -normalmente dos- que deben ser ponderadas, por ejemplo, las ventas en unidades y las líneas asociadas. El algoritmo K-ésimo puede considerarse una variante del método del alpinista ( hill climbing ), aunque con un enfoque un poco diferente. Estas fórmulas de clasificación, más o menos mejoradas, han sido enormemente útiles hasta la fecha, a la hora de optimizar la disposición de los artículos en el lay out del almacén, pero con la aparición de la Inteligencia Artificial se suman nuevas posibilidades en la optimización de dicho posicionamiento de los artículos y se eliminan defectos intrínsecos del análisis ABC, como la ausencia de consideración en los cálculos de la denominada Correlación de Artículos . Para entender este término de correlación lo mejor es explicarlo con un par de ejemplos: En un almacén de productos de alimentación se reciben pedidos de aceite de los diferentes supermercados en los que, por citar un producto de alto consumo, se solicita siempre aceite en gran cantidad y vinagre en una muchísima menor cantidad, lo que, con la interpretación ABC tradicional , nos llevaría a ubicar el aceite en posiciones A y el vinagre en posiciones C . Sin embargo, un enfoque más minucioso como el proporcionado por algoritmos de Inteligencia Artificial, como el algoritmo genético , nos puede llevar a concluir que, aunque en cantidades muy distintas, ambos artículos se encuentran correlacionados, es decir que siempre o prácticamente siempre que se pide uno, se pide el otro , lo que debería llevarnos a plantear una reubicación del vinagre en posiciones mucho más cercanas a las destinadas a los productos A. Algo idéntico ocurre en el caso de fabricantes de mercería , y que detectamos concretamente en uno de nuestros clientes de Dimensia, donde en los pedidos de hilo blanco o negro, en grandes cantidades dado que también son productos de enorme consumo en ese segmento, siempre (y la clave es de nuevo la palabra “siempre”) van acompañados de peticiones de hilo rojo, aunque en mucha menor cantidad (es un producto C en volumen de venta), por lo que están correlacionados y por tanto esta correlación será tenida en consideración por el algoritmo genético a la hora de tomar una decisión de posicionamiento.
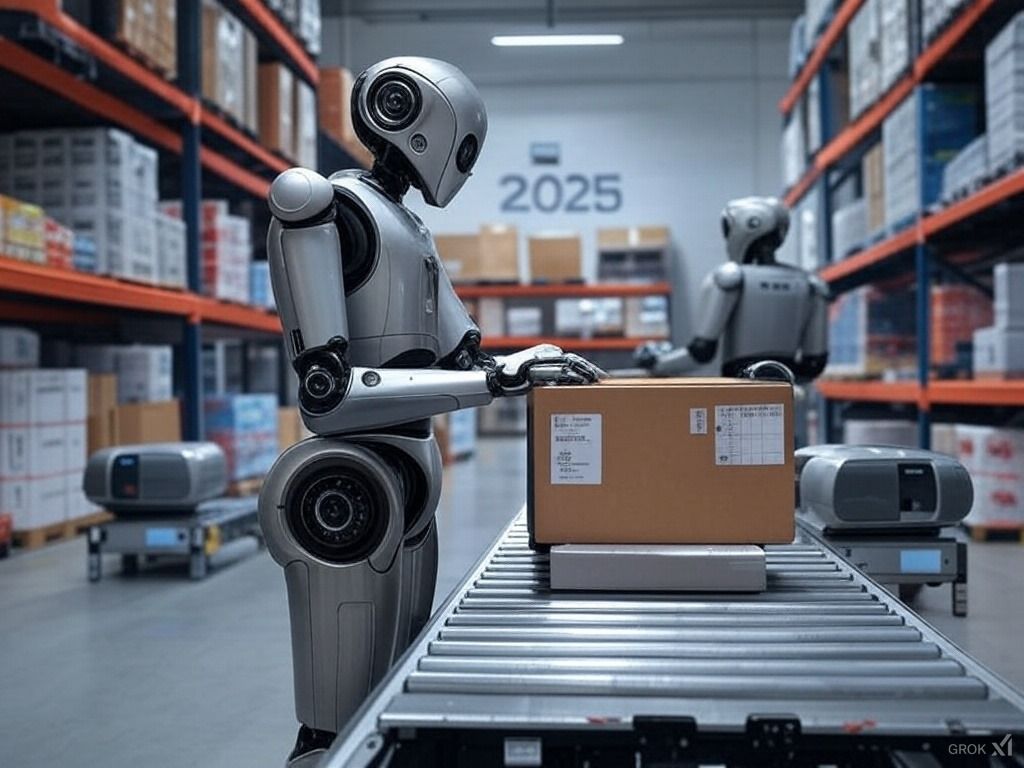
El año 2025 se perfila como un periodo de transformación significativa en el sector logístico en España. Diversos factores, como la digitalización, la sostenibilidad y la adaptación a nuevas normativas, están redefiniendo las operaciones logísticas y de transporte en el país. A continuación, detallamos las principales tendencias y novedades que creemos marcarán este año. 1. Digitalización e Inteligencia Artificial (IA): La integración de tecnologías avanzadas se ha convertido en una necesidad imperante para las empresas logísticas que buscan mantener su competitividad. La adopción de soluciones basadas en datos, como la inteligencia artificial y el análisis predictivo, permite optimizar rutas de entrega, gestionar inventarios en tiempo real y anticipar demandas del mercado. Esta transformación digital no solo mejora la eficiencia operativa, sino que también responde a las crecientes expectativas de los clientes en cuanto a rapidez y flexibilidad en las entregas. La IA también está optimizando la atención al cliente mediante chatbots inteligentes que gestionan consultas sobre envíos, devoluciones y seguimiento de paquetes, mejorando la experiencia del usuario y reduciendo carga operativa en los call centers y a tecnología blockchain está mejorando la trazabilidad y seguridad en la cadena de suministro dado que permite registrar cada movimiento de un producto de forma inmutable y transparente. 2. Sostenibilidad y Logística Verde: La conciencia medioambiental está impulsando al sector hacia prácticas más sostenibles. La implementación de flotas de vehículos eléctricos, el uso de energías renovables en almacenes y centros de distribución, y la optimización de rutas para reducir emisiones de CO₂ son algunas de las iniciativas que se están adoptando. Además, la economía circular gana terreno, promoviendo el reciclaje y la reutilización de materiales para minimizar residuos. Normativas como la Ley de Residuos y Suelos Contaminados están impulsando la adopción de certificaciones ambientales como ISO 14001 o sellos de huella de carbono cero. Muchas empresas están incorporando políticas ESG (medioambientales, sociales y de gobernanza) para cumplir con estas exigencias. 3. Innovaciones en la Última Milla: La última milla, o el tramo final en la entrega de productos al cliente, sigue siendo uno de los mayores desafíos logísticos. Para abordar este reto, se están explorando soluciones innovadoras como el uso de drones y vehículos autónomos para entregas rápidas y eficientes. Además, la implementación de puntos de recogida automatizados y lockers inteligentes en áreas urbanas facilita la entrega y recogida de paquetes, mejorando la experiencia del cliente y reduciendo la congestión en las ciudades. 4. Adaptación a Nuevas Normativas: El marco regulatorio en España está evolucionando para adaptarse a las demandas actuales del sector. Un ejemplo destacado es la implementación del nuevo impuesto de basuras que entrará en vigor en abril de 2025, afectando a todos los municipios con más de 5.000 habitantes. Esta medida busca que la gestión de residuos refleje su costo real, incentivando prácticas más sostenibles en la generación y manejo de desechos. Las empresas logísticas deberán mejorar su control y segregación de residuos para reducir su factura. La correcta separación de materiales reciclables y la disminución de residuos no reutilizables se volverá una prioridad para optimizar costos. 5. Desarrollo de Infraestructuras Estratégicas: La inversión en infraestructuras logísticas es clave para mejorar la eficiencia y conectividad del sector. Proyectos como la Base Logística del Ejército de Tierra en Córdoba, cuya urbanización se prevé concluir en junio de 2025, representan avances significativos. Esta instalación moderna y sostenible, que aspira a obtener un sello Breeam con el que se reconozca el cumplimiento de criterios de sostenibilidad ambiental, albergará 34 edificios en 86 hectáreas, centralizando actividades logísticas y mejorando la operatividad del Ejército. 6. Formación y Atracción de Talento: La escasez de personal cualificado, especialmente de conductores de camiones y personal especializado en logística, es una preocupación creciente. Para abordar este desafío, las empresas están invirtiendo en programas de formación y capacitación, así como en la mejora de las condiciones laborales, con el objetivo de atraer y retener talento joven en el sector. 7. Expansión del Comercio Electrónico: El comercio electrónico continúa su crecimiento en España, impulsando la demanda de servicios logísticos más ágiles y eficientes. Se estima que en 2025 el e-commerce crecerá un 5,4%, lo que obligará a las empresas logísticas a realizar inversiones significativas en infraestructura y tecnología para satisfacer las expectativas de los consumidores en cuanto a tiempos de entrega y flexibilidad. En resumen, el sector logístico en España en 2025 estará marcado por una profunda transformación impulsada por la digitalización, la sostenibilidad y la adaptación a nuevas normativas. Las empresas que adopten estas tendencias y se anticipen a los desafíos futuros estarán mejor posicionadas para competir en un mercado dinámico y en constante evolución.
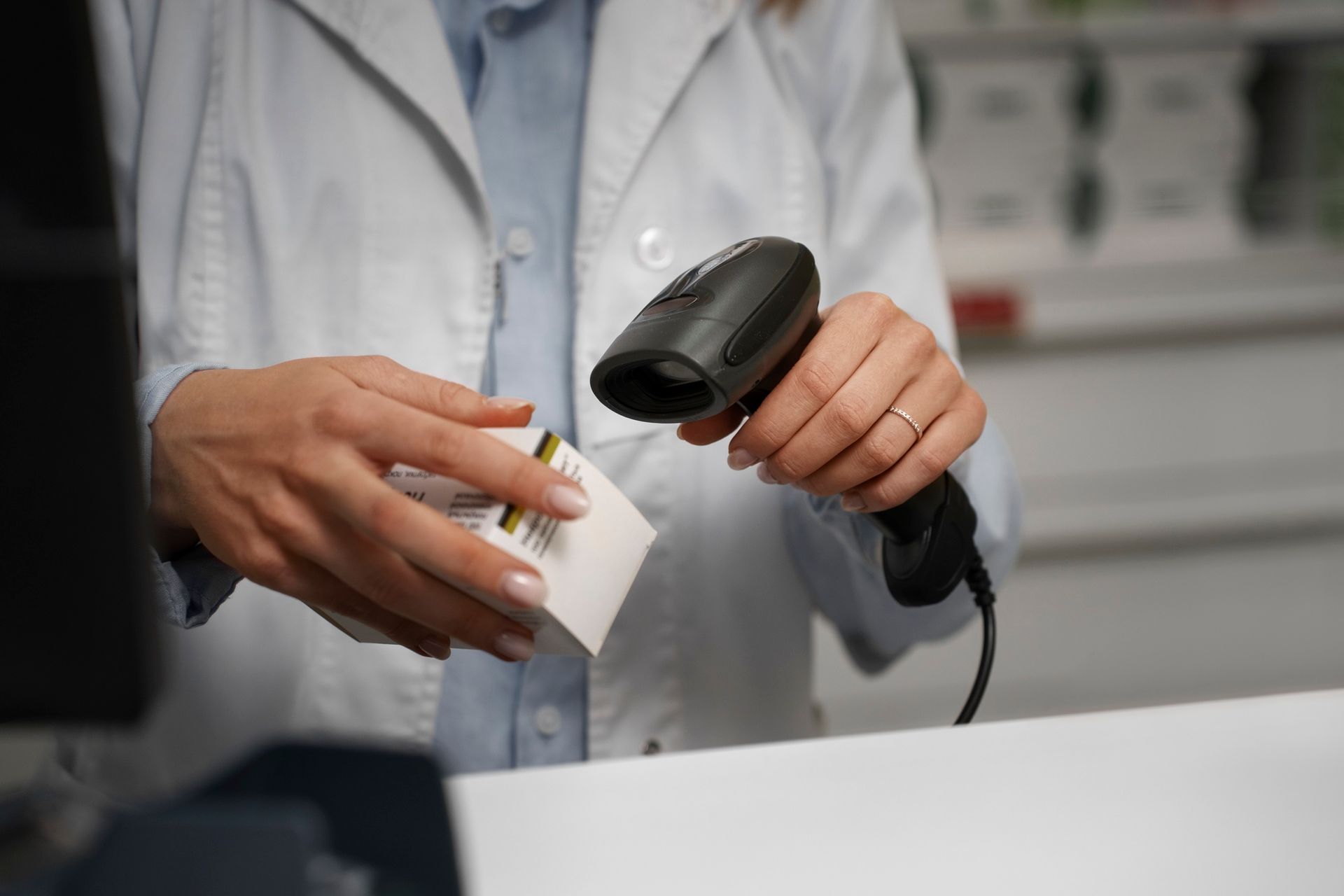
La recogida de pedidos en almacenes es sin duda una de las actividades más críticas en la cadena de suministro. La eficiencia y la precisión en este proceso tienen un impacto directo en la satisfacción del cliente y en la rentabilidad de la operación. En este contexto, la tecnología de radiofrecuencia (RF) ha emergido como una solución clave para optimizar esta tarea, especialmente en sectores donde la trazabilidad y la precisión son esenciales para cumplir con las regulaciones existentes y garantizar la entrega correcta de mercancías. ¿Qué es la radiofrecuencia y cómo se usa en almacenes? La tecnología de radiofrecuencia utiliza dispositivos móviles que se conectan de manera inalámbrica a un SGA o Sistema de Gestión de Almacenes (WMS, por sus siglas en inglés). Estos dispositivos, como lectores de códigos de barras, escáneres portátiles o terminales de datos, permiten a los operarios interactuar con el sistema en tiempo real.
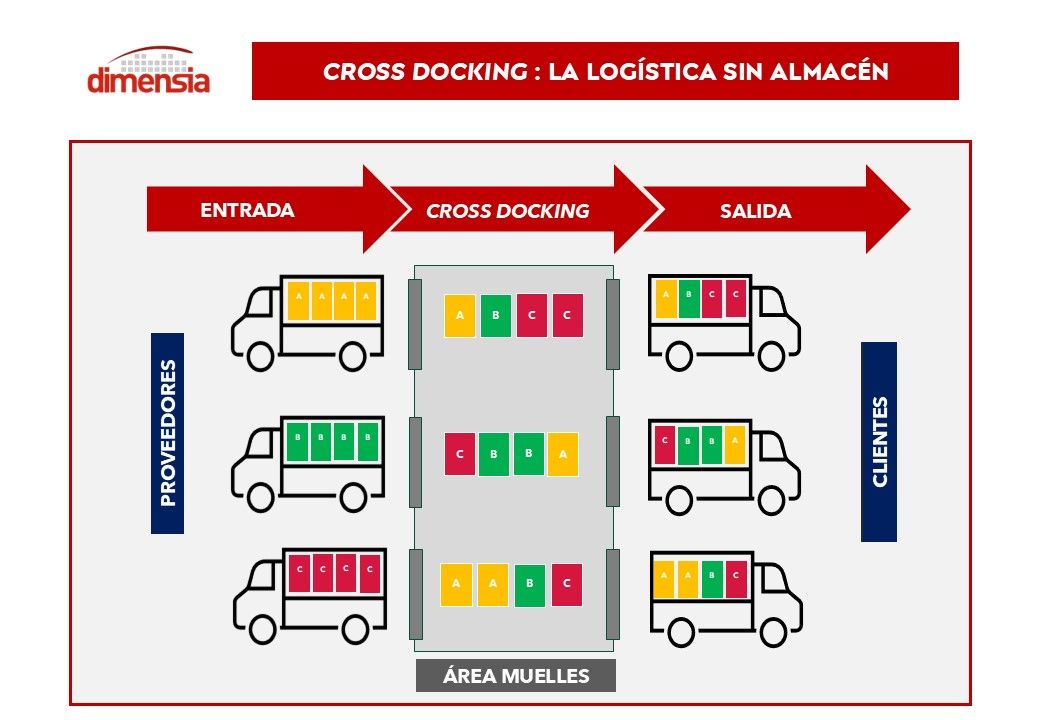
El cross docking es un procedimiento logístico que, esencialmente, consiste en el envío directo a los clientes de los productos que recepcionamos en nuestros almacenes mediante un “cruce de muelles” y, por tanto, sin pasar por un almacenamiento previo y controlado por el Sistema de Gestión de Almacén (SGA). En su versión más pura, no existiría manipulación alguna de los productos recepcionados que, simplemente, pasarían de un muelle de entrada a uno de salida para su envío a los clientes, en un formato que se denomina habitualmente pre-distribuido o directo. Sin embargo, las modalidades más habituales de cross docking , explotando al máximo las posibilidades de los SGA, conllevan la existencia de una superficie específica en el área de recepción-expedición y la manipulación de productos en operaciones de consolidación o desconsolidación. Operaciones que pueden referirse tanto a los productos recibidos como a los productos que se encuentran almacenados en nuestras instalaciones.
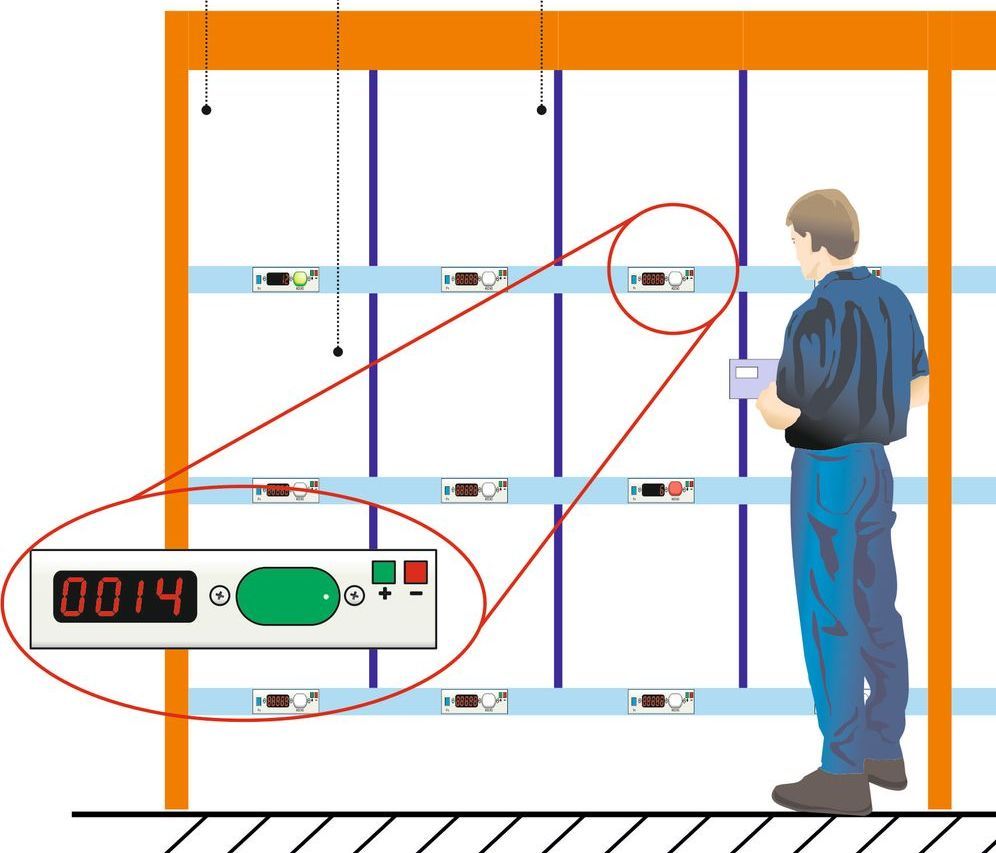
El “ pick to light ”, es un sistema de preparación de pedidos compuesto por un conjunto de estanterías dinámicas con displays , cuyo cometido es indicar de forma visual, al operario encargado del picking , el lugar al que se debe dirigir, que es la ubicación donde se encuentra el siguiente artículo que tiene que recoger. Adicionalmente, el visor encendido muestra el número de unidades a picar. El sistema pick to light es una tecnología innovadora que ha revolucionado la forma en que se gestionan los almacenes y centros de distribución en nuestro país y en todo el mundo. La utilización de estas luces y pantallas LED para guiar a los operarios en la preparación de pedidos, mejora de forma extraordinaria la productividad, eficiencia y precisión en el proceso de picking , evitando casi completamente los errores en el proceso. En España, este sistema ha experimentado un notable desarrollo en los últimos años, siendo cada vez más utilizado por empresas de los más diversos sectores.
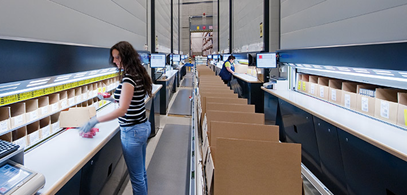
Entre las múltiples posibilidades que existen en la actualidad para la preparación de pedidos automatizada bajo la estrategia “producto a hombre”, se encuentran los carruseles verticales, también conocidos como paternóster. Los carruseles verticales están formados por una estructura cerrada de acero, con poca profundidad, pero gran altura, que integra un elevador motorizado y en cuyo interior se encuentran una serie de baldas rotativas en las que se ubican los productos. La parte inferior de esta estructura se encuentra abierta en una ventana de trabajo o abertura de servicio, de forma que el operario que se encuentra utilizándolo pueda extraer fácilmente el contenido de las bandejas durante la preparación del pedido.